Copper, a metal of unparalleled versatility, has captivated industries for centuries. Its alloys boast a myriad of exceptional properties, each contributing to their indispensable role in various applications. This blog embarks on an exploration of the remarkable attributes that define copper alloys, spotlighting their corrosion resistance, electrical conductivity, surface oxidation, yield strength, joining methods, hot and cold working capabilities, temper levels, casting nature, and designations.
Corrosion Resistance: In the world of materials, corrosion resistance is a prized quality. Copper alloys, the epitome of durability, exhibit remarkable resistance to corrosion in a range of environments. From fresh water and steam to rural, marine, and industrial atmospheres, these alloys stand strong. Their resilience extends to saline solutions, soils, non-oxidizing minerals, organic acids, and caustic solutions. However, challenges arise when exposed to corrosive agents like halogens, moist ammonia, sulphides, ammonia-ion-containing solutions, and strong oxidizing acids. While copper alloys generally struggle against inorganic acids, certain ones, such as Copper Nickel alloys, Aluminium Brass, and Aluminium Bronzes, display a superior resistance to saltwater corrosion. The secret to their corrosion resilience lies in the formation of protective adherent films on their surfaces, effectively shielding the base metal from further degradation.
Electrical Conductivity: Copper’s electrical conductivity is a marvel, ranking second only to silver. With 97% of silver’s conductivity, copper has historically been the go-to material for electricity transmission. However, in high-voltage power lines, weight considerations have propelled the use of aluminum due to its significantly lower density. Aluminum alloys, with nearly twice the conductivity of copper by weight, play a crucial role. While they may lack the strength of copper, reinforcement through galvanized or aluminum-coated high tensile steel wires ensures their performance. Though the addition of elements like cadmium can enhance their strength, it comes at the cost of decreased electrical conductivity.
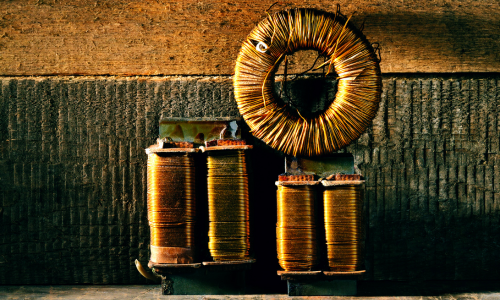
Surface Oxidation and Patination: Copper alloys gracefully age with exposure to the elements, developing distinctive hues that tell a tale of their journey. The iconic blue-green patina adorning most copper alloys outdoors resonates with the Statue of Liberty’s verdigris color in New York. Over time, some alloys transform to shades of brown and black, showcasing their endurance. To preserve their original allure, lacquer coatings come to the rescue, safeguarding the surface and maintaining the alloy’s initial color. An acrylic coating, fortified with benzotriazole, emerges as a reliable choice, promising years of protection under outdoor, abrasion-free conditions.
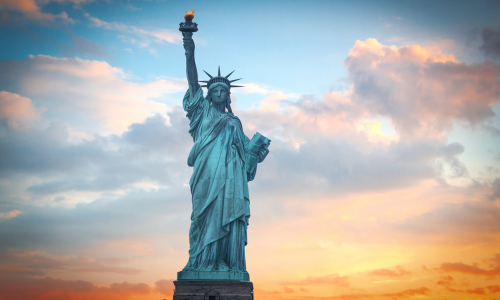
Yield Strength and Joining: Copper alloys possess a yield point that isn’t rigidly defined, often reported as either a 0.5% extension under load or a 0.2% offset. Joining these alloys is facilitated through common methods such as brazing, welding, and soldering. Soldering takes center stage for electrical connections, while high lead-content alloys steer clear of welding due to their unsuitability. In addition to traditional methods, mechanical means like rivets and screws provide alternative paths for uniting copper alloys.

Conclusion: Copper alloys stand as a testament to engineering prowess, embodying qualities that propel industries forward. Their corrosion resistance, electrical conductivity, and other diverse attributes paint a portrait of adaptability and endurance. From infrastructure to electronics, these alloys leave an indelible mark, enriching lives and shaping a world built on innovation.
One comment
Nice post. I was checking constantly this weblog and I am impressed!
Extremely helpful info specifically the remaining phase 🙂 I take care of such information much.
I used to be seeking this particular information for a
very long time. Thanks and best of luck.