Understanding common defects in seamless pipes is essential for maintaining product quality and integrity. Let’s explore these defects, their characteristics, and the underlying causes that can impact seamless pipe manufacturing.
1. Abscission:
Defect Characteristics: Spiral separation or rupture on the inner surface resembling a metal sandwich.
Causes: Poor non-metallic inclusions, residual shrinkage, or severe osteoporosis in the material.
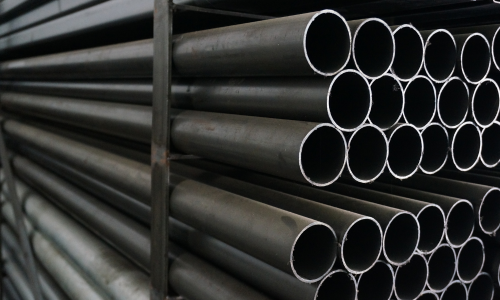
2. Straight Fold Within:
Defect Characteristics: Symmetrical or single linear folding on the inner surface.
Causes: Inadequate mandrel lubrication, mandrel surface defects, scrap iron intrusion, rolling process inadequacies.
3. Wall Contraction:
Defect Characteristics: Local thinning of the wall thickness, forming surface depressions.
Causes: Improper pressure adjustments, unreasonable extension coefficient distribution during rolling.
4. Rolling Scars Within:
Defect Characteristics: Vertical nail-shaped scars, raised or block folding.
Causes: Poor mandrel lubrication, local wear, damage, metal sticking, lack of meat, or large cracks.
5. Rolling Fold:
Defect Characteristics: Apparent grooves, concave or convex folds on the inner surface.
Causes: Excessive waste pipe diameter, poor control, weak bamboo, inadequate lubrication, rolling mill speed errors.
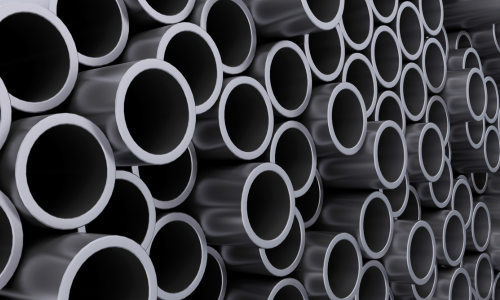
6. Double Seam Fold:
Defect Characteristics: Scattered or symmetrical cracks on the surface.
Causes: Irregular diameter, capillary diameter, or folding-related issues.
Conclusion: Identifying and understanding these seamless pipe defects is crucial for ensuring high-quality products. By addressing their root causes, manufacturers can implement measures to enhance the seamless pipe production process and uphold industry standards. Choose seamless pipes manufactured with precision and meticulous quality control to ensure superior performance and reliability.